Hydro jetting relies on high-pressure water to blast away clogs and other debris from pipes. Before hydro jetting, plumbing professionals use a video inspection to identify weak spots and select the appropriate nozzle type and water pressure for safe and effective cleaning.
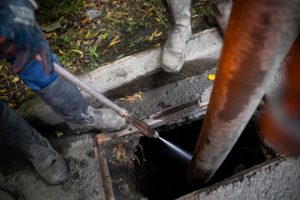
Home sewer lines work hard to safely carry waste to the city sewer line, but they’re vulnerable to clogs. Keep reading the article below to learn more about Hydro Jetting Sewer Line.
While many drain cleaning options rely on harsh chemicals, hydro jetting uses water to thoroughly clean pipes and eliminate obstructions. This process can be used on a variety of pipe materials and is highly effective against hardened fat buildups, roots, debris and more. It is also ideal for long runs of pipe, as it can clear out even the most stubborn blockages without requiring excavation.
Before beginning the process, a plumbing professional will use a video inspection to assess the severity of your clog and pinpoint its location. They will then set up the water jet machine, which will feed forceful streams of water into your sewer line via an access port or existing drain opening. The nozzle on the end of the hose can be switched between different types, allowing plumbers to target specific types of debris. For example, the chisel-type nozzle can cut through clogs and roots while the pulverizer-type nozzle blasts away sludge and debris.
When used properly, this method can remove most obstructions in your sewer lines, including fat, sludge, paper, food waste and other common causes of blocked drains. It can also reduce the coefficient of friction on pipe walls, minimizing the likelihood that new blockages will form. In fact, many residential and commercial clients have this service performed on a routine basis to prevent costly and disruptive clogs. Foul odors coming from your sinks and toilets, or bubbling or gurgling sounds in your drains, are often signs of partial or full clogs. Hydro jetting effectively scrubs these residues away, restoring normal flow and eliminating odors. This service is also useful for removing mineral deposits like lime scale, which can interfere with water flow and cause clogs.
No Chemicals
Traditional methods can leave behind chemical residue and push clogs deeper into the pipes. Hydro jetting does not use chemicals in the cleaning process, which makes it better for the environment and your home’s plumbing.
In addition to being safer for your home, hydro jetting is quicker than traditional methods. The high-pressure water jets blast away debris and clogs with little effort, saving time for your plumber. This method also eliminates the risk of sewage coming into contact with surfaces in your home or yard, which is a concern with other traditional clog removal techniques.
The power of water also works well on a wide variety of materials. Soap scum and hair can create soft but stubborn clogs, which are easily dislodged with hydro jetting’s rear-facing jets. Paper products and even so-called “flushable” wipes can clog older pipes. These items can form a thick, sticky clump when combined with grease or sludge. Hydro jetting’s powerful jets can dissolve these tough materials quickly and without harsh chemicals.
In addition, hydro jetting cleans the interior walls of your pipes. This helps prevent future blockages from occurring, and it allows you to get a clear view of your sewer line during a video inspection or any repairs. If your older pipes are prone to rusting or developing scale, hydro jetting can remove years of buildup and restore their structural integrity. The water jets can also remove tree roots that may be infiltrating the pipes, leading to a sewer backup. The process also removes odor-causing buildup, which leaves your pipes smelling fresh and clean.
Non-Invasive
Whether you’re a homeowner frustrated with repeat clogs, a commercial property owner trying to maintain health code compliance, or a property professional protecting an aging infrastructure, non-invasive sewer repairs are your best option. Unlike traditional methods, which require extensive digging and property disruption, hydro jetting uses water power to restore pipes.
This method involves feeding a hose into the sewer line through a cleanout, a designated access point usually located on the property’s exterior. The nozzle on the end of the hose shoots a high-pressure jet of water at obstructions and clogs to break them apart and blast them away. As the water jet travels through the pipe, it scourges the entire length of the pipe walls, leaving behind a smooth, debris-free surface that minimizes future blockages and ensures wastewater flows properly.
Hydro jetting is particularly effective at removing tree roots from sewer lines. As the water jet scours the pipe walls, it slices through any infiltrating tree roots and pushes them away from the line, saving you from costly sewer repair or replacement.
Frequent clogs, slow draining, gurgling pipes, and foul sewer odors indicate there’s a buildup of grease rings, mineral scale, hair mats, or tree roots that basic tools can’t dislodge. A full hydro jetting session typically takes about 30 to 60 minutes, depending on the severity of the clog and the length and diameter of the pipes.
A non-invasive sewer solution like hydro jetting can keep your plumbing flowing smoothly and protect your home or business from expensive damages caused by a broken sewer line. Contact us to learn more about our services and schedule a free consultation today! We proudly serve the greater Seattle area.
Safe for All Pipe Materials
While PVC and HDPE plastic pipes are the preferred piping materials in new homes, many older homes still use clay, cast iron or Orangeburg pipes. These pipes are far less durable than the modern alternatives and are prone to clogs and blockages. The good news is that hydro jetting can safely clean these old pipes, too. The pressurized water used during this process is strong enough to dislodge stubborn clogs but gentle enough to wash away any harmful residue or debris.
The key to safe hydro jetting is working with a professional plumbing company. A skilled plumber will conduct a thorough inspection of the piping system and adjust the pressure levels accordingly to prevent damage. They will also check the condition of the pipes using a video camera to spot any weak spots or existing damage that require special attention.
Even if you’re careful to flush your toilets and drain waste according to the recommended guidelines, sewer line clogs can still occur. The main culprit is usually invasive tree roots that grow toward the pipelines in search of water. As the roots latch onto the lining of the pipe, they can form dense blockages that cause slow drains and recurring backups. Unlike traditional rooter services, which just punch a hole in the clog, hydro jetting completely clears the clogged pipe.
The high-pressure water stream that is delivered through the nozzle can cut through stubborn clogs and tree roots with ease. However, if the underlying pipe is in poor condition, it may be damaged during this process. This is why plumbers always conduct a video inspection before hydro jetting. This allows them to see the condition of the pipes and determine whether or not hydro jetting is appropriate for them.
Preventative Maintenance
Clogged pipes can cause a variety of problems for homeowners and businesses, including plumbing backups and property damage. Using high-powered water jets, hydro jetting breaks up and washes away debris from the entire interior of pipes, restoring proper flow and preventing future blockages. This method is also a safe and environmentally conscious alternative to other drain line cleaning services like rooter and auger drain cleaners, which use rotating cables to dislodge pipe clogs.
A plumbing professional inserts the nozzle of a hydro jetting rig into the access port (also known as your sewer cleanout) at your home or business, then turns on the system to send out powerful water jets. The nozzles are designed to target specific types of debris, including accumulated grease and mineral buildup, intrusive tree roots, silt and sand deposits, and other obstructions. Your plumber will adjust the water pressure based on your pipes’ condition and material to ensure safe, effective cleaning.
To get started, your plumber will inspect the clogged pipe using a camera to determine the type and severity of the obstruction. The camera helps to identify the blockage’s source and select the right nozzle and water pressure to effectively break up and wash away the debris. It also allows the plumber to check for any damage or weakened areas in your pipes that may rupture under high water pressure.
After the clog is fully cleared, your plumber will check again with the camera to confirm that the pipes are clean. This step reveals any issues that need to be addressed, such as damaged or weakened sections of your pipe, and provides you with a full report on the hydro jetting process.